Manufacturing Processes
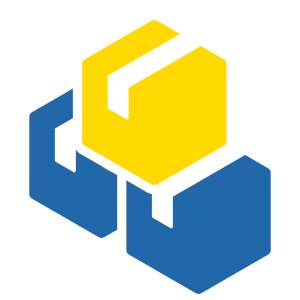

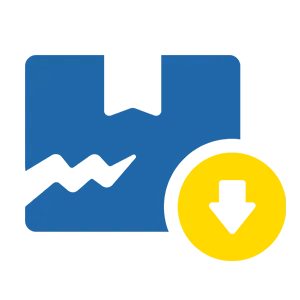
of Defective Products
Production Processes of Our Plastic Closures
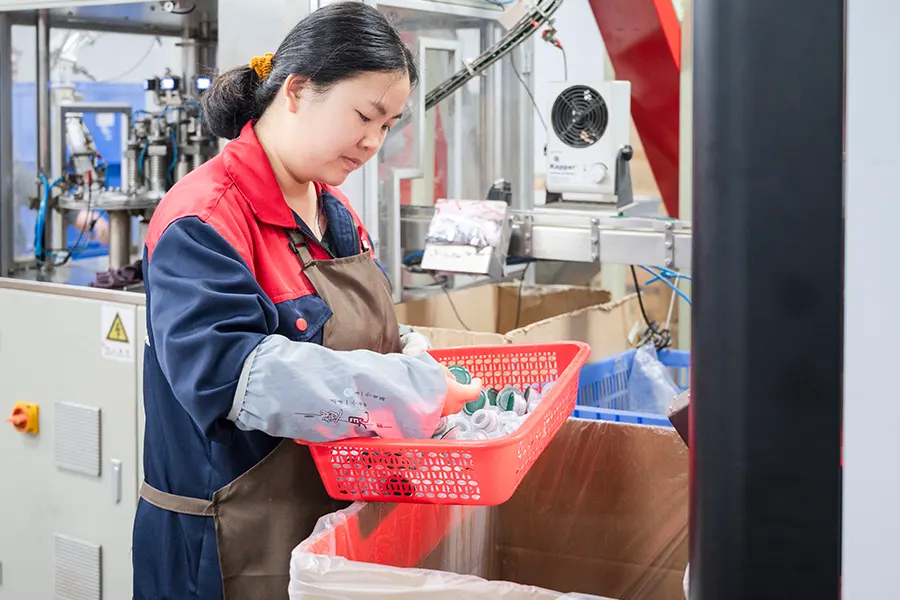
Raw Material Selection and Preparation
We source premium-grade plastic materials from trusted suppliers like Sinopec, ensuring consistency and compliance with global standards. Materials are inspected and prepared for the molding process to meet specific production requirements and they are all tracable.
Injection or Blow Molding
Adopting advanced Haitian injection machines and state-of-the-art blow molding technology, we shape the raw materials into precise specifications to ensure consistent fitting and functionality.
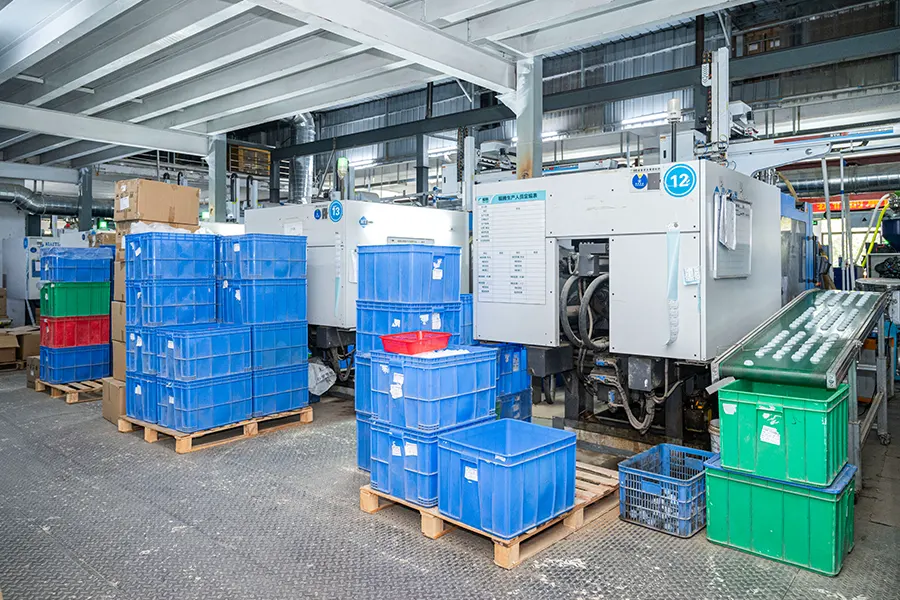
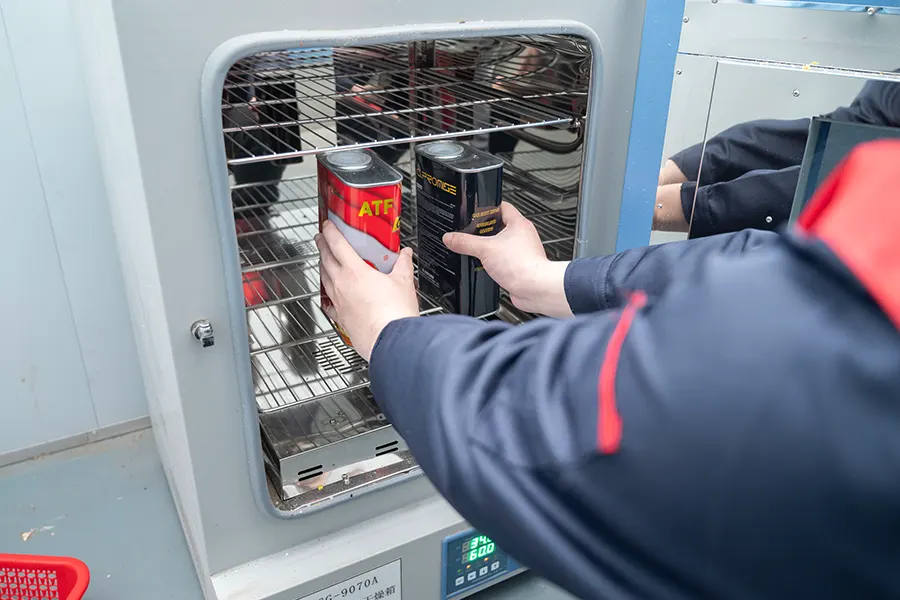
Cooling and Hardening
The molded caps are cooled using controlled temperature systems, solidifying their shape and enhancing their structural integrity to ensure durability and dimensional accuracy of the caps.
Automated Assembly
18 automated assembly machines streamline the assembly process, increasing efficiency while keeping your caps strong and durable, maintaining quality during transportation and use.
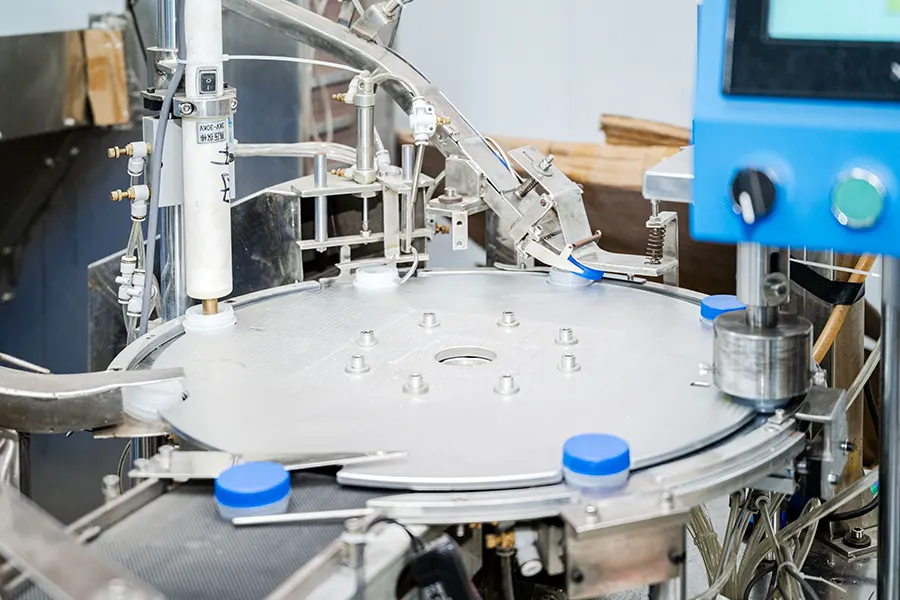
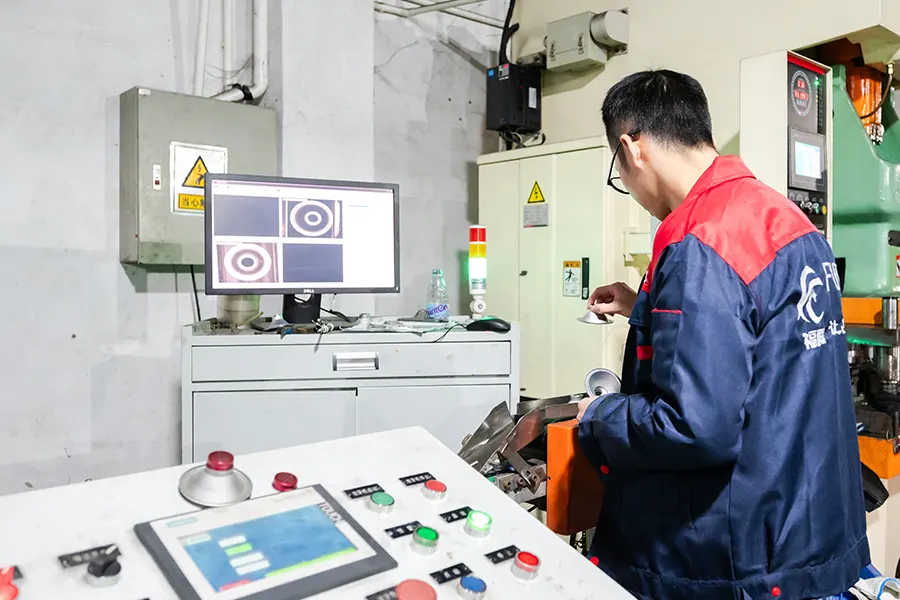
Testings and Inspections
We validate closure quality consistency through a 3-round quality control process. The first is a full run quality check of the raw materials, and the second round utilizes state-of-the-art automated testing equipment to ensure that all closures meet the highest standards of sealability. We double-check semi-finished products every hour, adhering to strict standards, and perform a final full batch inspection after assembly to ensure that the product received meets your high quality expectations and end use.
Packaging, Storage, and Delivery
The closures are securely packaged, labeled and stored in our clean warehouse. Once your order is confirmed, we deliver your safe-packaged closures on time and with reliability, ready for seamless integration into your supply chain.
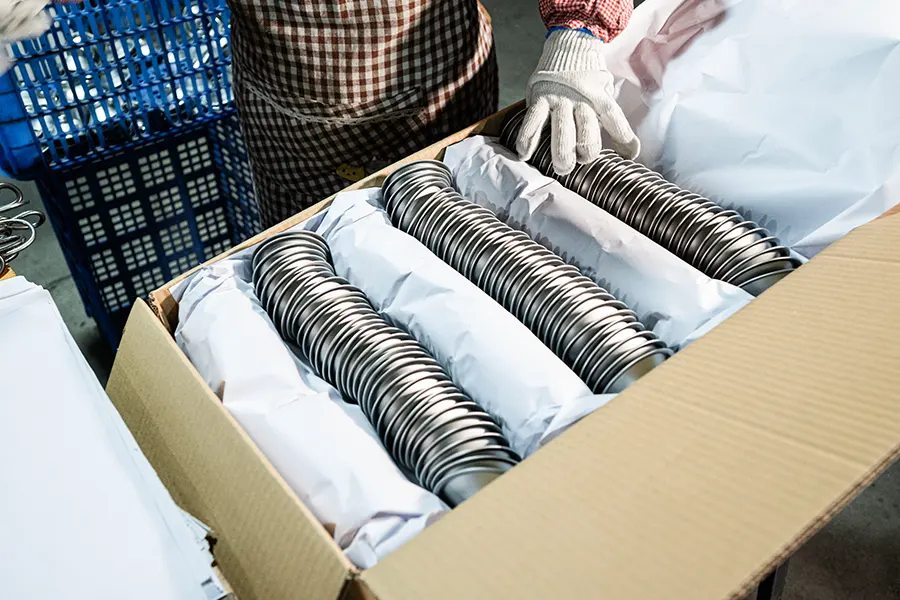